ESAMI 2012 DISEGNO DI CARROZZERIA_Dal secondo gruppo di studenti di Ingegneria del Veicolo, ecco la Ferrari SS, sempre dedicata a Scaglietti
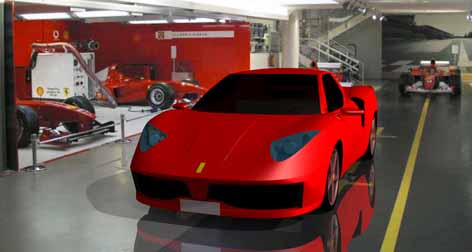
SCARICA LA TESINA COMPLETA
FACOLTÀ DI INGEGNERIA “ENZO FERRARI” CORSO DI LAUREA MAGISTRALE IN INGEGNERIA DEL VEICOLO
CORSO DI “DISEGNO DI CARROZZERIA E COMPONENTI”
DOCENTE:
Prof. Fabrizio FERRARI
STUDENTI:
Alessandro Berti, Sebastiano Breda, Nicola Giovannoni, Alessandro Iobbi
ANNO ACCADEMICO 2011-2012
Il progetto della carrozzeria che equipaggia la
Ferrari SS parte dall’idea di rivisitare lo storico
modello Ferrari 250 Le Mans Berlinetta 1964,
sviluppando una berlinetta due posti con motore
centrale, in onore a Sergio Scaglietti, Designer di
carrozzeria legato alla storia della prestigiosa
azienda automobilistica di Maranello.
Il lavoro assegnato poteva essere interpretato in più modi: il restyling infatti è una operazione
delle case produttrici di automobili che si basa sul successo del modello di partenza già presente
sul mercato, e può essere svolto ammodernando le linee già definite di una vettura (spesso
praticato su vetture di produzione recente), o ridisegnandola completamente in chiave moderna
(orientata alla rievocazione di vetture più datate).
Nello sviluppo del nostro progetto abbiamo seguito la seconda strada: infatti è prevalsa l’idea di
realizzare uno stile completamente nuovo che richiamasse però in alcuni dettagli ben definiti il
modello di ispirazione, piuttosto che procedere al restyling basandosi sulla linea già definita dal
modello del 1964.
Il progetto è partito da un layout base di riferimento che simula i principali ingombri di una vettura
stradale della categoria berlinetta/2 posti: il gruppo propulsore-trasmissione in posizione centrale,
le ruote e i relativi organi di sospensione, parte del telaio, sterzo e pedaliera.
Da un lato è stata posta l’attenzione allo stile: seguendo il tipico iter per la progettazione di una
carrozzeria siamo partiti da semplici idee stilistiche, disegnando bozzetti a mano della vettura vista
in più angolazioni, senza farci limitare dai vincoli tecnici. In questa fase infatti l’obiettivo è quello di
ottenere una riproduzione più qualitativa che quantitativa, che definisca l’estetica della vettura
cosi come concepita dalla mente creativa del designer. Dall’altro lato a partire dal layout fornito
sono stati definiti i principali punti cruciali nel rispetto delle norme di omologazione: il
posizionamento del manichino Oscar, la localizzazione dei gruppi ottici all’anteriore e al
posteriore, gli ingombri di massima della vettura, il posizionamento delle parti mobili. Questa fase
pone l’attenzione sul piano dell’engineering e della sicurezza, dato che il concept iniziale andrà
ottimizzato, verificato e vagliato più volte in ogni suo aspetto, finchè non saranno soddisfatti tutti
i requisiti fondamentali di sicurezza, di omologazione e di produzione (su piccola o larga scala, in
base alla categoria di appartenenza della vettura). Un ulteriore aspetto di fondamentale
importanza è rappresentato dalla possibilità di svolgere le attività servendosi degli strumenti
CAD/CAE, secondo il moderno approccio di progettazione industriale: In particolare la
modellazione 3D della carrozzeria, a partire dai dati di un disegno tecnico 2D, permette di
superare i limiti della rappresentazione in proiezione, ottimizza i tempi di modifica degli elementi
del progetto, permette di eseguire verifiche sull’accoppiamento e sui cinematismi degli elementi e,
in un’eventuale fase di produzione, permette di implementare simulazioni e ottenere dati gestibili
direttamente dai sistemi di produzione. Il fulcro del successo di tale lavoro quindi sarà quello di
creare il giusto connubio tra tecnica e stile, trattandosi di un prodotto (la carrozzeria) di forte
impatto visivo e allo stesso tempo di complessità funzionale, laddove si interfaccia col resto del
veicolo e con il conducente e i passeggeri.
1. Scelte stilistiche e primi bozzetti
La prima fase del progetto prevede una delle attività più importanti: la scelta dello stile della
futura vettura. Per questo abbiamo realizzato alcuni bozzetti di stile fatti a mano (Figura 1.1),
valutando le diverse alternative proposte dai membri del gruppo, per arrivare alla scelta del
concept di partenza.
Dal concept scelto (Figura 1.2) si nota immediatamente, rispetto alla 250 Le Mans, una
rielaborazione della disposizione dei volumi, in modo da uniformare e snellire il profilo che dal
musetto corre su tutto il veicolo fino alla coda, questo grazie al prolungamento e l’ispessimento
delle vele laterali che costeggiano il vano motore. I gruppi ottici si mantengono tondi al
posteriore, rispettando il family feeling di casa Ferrari, mentre all’anteriore assumono una forma
più tagliata, con spigoli vivi che rendono più moderne le linee del frontale della vettura. Le prese
d’aria del vano motore vengono mantenute nella loro posizione originale, ma riviste nella forma e
nelle dimensioni.
Sul paraurti anteriore viene mantenuta l’apertura centrale, ma suddivisa in due parti, mentre sul
cofano sono previsti due sfoghi simmetrici (non presenti nel modello del 1964) per favorire
eventuali flussi d’aria in uscita.
Nella parte posteriore è stato pensato fin da subito di inserire un estrattore, sia per motivi estetici
che funzionali.
2. Analisi del layout di base
2.1. Definizione degli ingombri generali
I primi vincoli dal punto di vista tecnico sono stati dettati dal layout meccanico di base fornitoci dal
docente (Figura 2.1); esso infatti impone alcune delle principali dimensioni (passo= 2560 mm,
carreggiata anteriore= 1590 mm , carreggiata posteriore=1576 mm ) e definisce i limiti minimi
degli ingombri totali del veicolo, per garantire la copertura e la protezione dei principali organi
meccanici.
2.2. Oscar: posizionamento e verifiche per l’omologazione
Dall’analisi preliminare del layout è subito emerso un posizionamento scorretto del manichino
Oscar, nonché dimensioni dello stesso non corrispondenti al 50 percentile.
Utilizzando un manichino dalle dimensioni conformi alla normativa, fornito dal docente, sono state
definite le quote del punto H relativo alla posizione del sedile (già fissato nel layout) nella
configurazione media di regolazione orizzontale e verticale, adattandolo opportunamente alla
pedaliera e evitando interferenze tra le gambe e il volante . Fissato il punto H è stata ricavata la
disposizione ottimale del tronco del manichino, con un’inclinazione rispetto alla verticale passante
per H di circa 5 gradi entro il limite di sicurezza regolamentare (25 gradi) e che garantisse una
giusta impugnatura del volante e della leva del cambio. Successivamente è stata tracciata la
traiettoria del punto più alto del casco ottenuta con una rotazione rigida del tronco attorno al
punto H, determinando lo spazio minimo necessario affinché, in caso di urto frontale il manichino
non venisse a contatto con il parabrezza o la parte inferiore del tetto. Dalla posizione del tronco e,
di conseguenza, della testa, sono state definite le coordinate del punto medio degli occhi (Figura
2.2).
Punto H: x= 1150 mm, y= 380 mm, z= 355 mm,
Punto medio occhi: x= 1280 mm, y= 380 mm, z= 1030 mm.
3. Generazione della carrozzeria
Una volta ottenuto un layout e una configurazione di Oscar definitivi, abbiamo potuto impostare
un piano di forma, ovvero una rappresentazione in scala (1:5) nelle quattro viste fondamentali in
proiezione ortogonale (vedi allegato “piano di forma su millimetrato”). La scelta della scala è stata
dettata dalla necessità di contenere quanto possibile le dimensioni del disegno, ma allo stesso
tempo di non perdere dettagli importanti in fase generativa. Al piano di forma è stato associato un
sistema di riferimento destrorso con origine all’intersezione tra il piano medio longitudinale della
vettura, il piano di terra e il piano verticale passante per l’assale anteriore, asse X orientato verso il
posteriore e asse Z verso l’alto.
In questa fase del progetto si è tenuto conto di tutti i vincoli progettuali imposti dalla normativa
inerenti agli elementi propri della carrozzeria, sul piano della sicurezza, dell’engineering o del
comfort; l’approccio è stato quello di adattare le singole parti affinché rientrassero nei vincoli
omologativi, senza però subordinare totalmente le scelte stilistiche alla regolamentazione. Inoltre
abbiamo mantenuto sempre un’impostazione critica generale sulla carrozzeria, preoccupandoci
che le modifiche isolate alle singole parti non alterassero l’armonia globale del prodotto. Inoltre
sono state vagliate dal gruppo alcune scelte che, anche se non direttamente imposte dalla
normativa, si rendono necessarie allorquando lo studio non vuole limitarsi ad un approccio
teorico, ma cerca di affrontare il più possibile ogni aspetto come in una vera e propria attività di
progettazione industriale.
3.1. Linee generali
I primi vincoli da imporre sono stati:
-altezza minima da terra di 12 cm, verificati dalla possibilità di far scorrere un parallelepipedo alto
12 cm sotto la vettura senza incontrare ostacoli,
-angoli di attacco e di uscita di almeno 7°, verificati dalla possibilità di percorrere una rampa con
inclinazione di 7° sia in salita che in discesa senza causare contatti della carrozzeria con il fondo
stradale,
-copertura completa di tutti gli organi meccanici,
-ingombro massimo delle ruote dovuto alla sterzatura delle ruote anteriori e allo scuotimento
delle quattro sospensioni;
C:\Users\Alessandro\Desktop\oscarstampa.jpg
Da questi e dai sopra citati vincoli dimensionali imposti dal layout è stata impostata la forma di
massima della carrozzeria, ovvero la linea del fondo, la forma del musetto e del paraurti posteriore
e la linea che corre dal cofano alla coda, definendo la forma del padiglione.
Dopo aver disegnato correttamente l’andamento del cofano nel rispetto dell’angolo di visibilità di
Oscar sul piano XZ, garantito di 7° su ogni punto, abbiamo notato che la compatibilità della linea
del parabrezza e del tetto con il movimento della testa di Oscar è risultata pressoché al limite.
Per queste ragioni il volume del padiglione è stato sbilanciato leggermente in avanti in modo da
rientrare in un margine di sicurezza sufficiente (considerando anche lo spessore inevitabile che si
ha tra la lamiera e il rivestimento interno del tetto). Questa scelta ha prodotto anche un risultato
vantaggioso: facendo avanzare il curvano, il parabrezza è risultato più proiettato in avanti e più
coerente con l’andamento del cofano, conferendo modernità alla linea. Ovviamente è
stato verificato che l’angolo di visibilità non fosse stato alterato da queste modifiche (Figura 3.1).
La forma del padiglione sul piano YZ (vista frontale) è stata disegnata in modo tale da avere una
larghezza quasi costante al variare dell’asse X, nel settore interessato dai cristalli laterali: il
corretto movimento di abbassamento infatti richiede una curvatura sul piano XY quasi nulla; la
curvatura sul piano YZ invece deve essere tale da permettere al cristallo di scorrere all’interno
della portiera senza essere ostacolato: da questo ne consegue un disegno coerente della portiera
sul piano YZ per tutta la sua estensione.
Definita la forma laterale del padiglione è stato necessario un controllo incrociato sulle distanze
minime da garantire tra testa di Oscar e cristallo laterale e spalla di Oscar e cristallo laterale, che
sono risultate soddisfatte.
La forma dei montanti tra parabrezza e cristalli laterali è stata definita dopo aver imposto il
vincolo sull’angolo di visuale del manichino Oscar sul piano XY passante per il punto medio degli
occhi:
-maggiore di 15° verso il montante sinistro,
-maggiore di 45° verso il montante destro.
Definiti i bordi dei cristalli laterali è stata disegnata la geometria della portiera, con apertura
classica, incernierata al bordo verticale anteriore, di forma tale da contenere l’intero cristallo in
posizione abbassata. La parte superiore delle portiere è stata prevista priva di giroporta, con il
cristallo a battuta direttamente sulla struttura del montante.
La parte retrostante del padiglione è stata realizzata enfatizzando la copertura del vano motore
della 250 LM: viene aggiunta la copertura trasparente e le vele laterali vengono ispessite e
prolungate verso la coda della vettura per dare continuità al padiglione. Tra di esse è stato ricavato
un pannello (all’altezza della parete tagliafiamma) che contiene il lunotto.
A questo punto è stata eseguita una prima modellazione 3D al CAD del layout di base, da cui
partire per modellare la carrozzeria, lavorando in parallelo sul 2D cartaceo e sul 3D. Il 2D infatti
fornisce i punti necessari alla costruzione tridimensionale delle features, mentre il 3D facilita le
eventuali modifiche successive.
3.2. Gruppi ottici anteriori
I vincoli inerenti ai gruppi ottici anteriori sono:
-uso del faro anabbagliante Hella fornito dal docente (Appendice 1),
-distanza minima tra le superfici interne dell’anabbagliante: 600 mm,
-distanza minima da terra dell’anabbagliante: 500 mm,
-distanza massima da terra dell’anabbagliante: 1200 mm,
-distanza minima dal fuori tutto anteriore dell’anabbagliante: 200 mm, ovvero l’area deformata in
caso di urto frontale, che non deve interessare gruppi ottici e parti mobili,
-distanza massima della superficie esterna dell’anabbagliante dal fuori tutto laterale: 400 mm,
-angolo di apertura del fascio luminoso sul piano XY di 10° verso l’interno e di 45° verso l’esterno,
-angolo di apertura del fascio luminoso sul piano XZ di 15° verso l’alto e 10° verso il basso, per
entrambi i fari.
-gli indicatori di direzione anteriori hanno le stesse limitazioni dell’anabbagliante riguardo alla
posizione trasversale, mentre la posizione verticale deve essere compresa tra 350 mm e 1500 mm,
– le luci abbaglianti non devono essere più lontane dell’anabbagliante dal piano longitudinale
medio.
Una volta disegnata la linea del gruppo ottico cosi come scelta sul bozzetto, e riportata nelle tre
proiezioni ortogonali è stato posizionato il faro anabbagliante Hella. Il primo posizionamento nella
vista frontale non causava interferenze tra l’ingombro del faro e le superfici esterne o le parti
interne, ma non rientrava nell’omologazione dato che il fascio aveva un cono di apertura sotto il
limite. Per questo il faro è stato traslato in direzione X e Y fino alla quota definitiva che verificasse
tutti i requisiti sopra citati (Figura 3.4).
Le restanti funzioni del gruppo ottico sono state inglobate in linea con l’anabbagliante, scegliendo
la classica tecnologia a lampadina anche per abbagliante e indicatore di direzione, mentre si è
deciso l’uso di una serie di led, molto diffuso negli ultimi tempi, per la funzione di luci di posizione,
situata lungo il bordo superiore del gruppo ottico.
Coordinate centro Anabbagliante: x= -545 mm, y= 650mm, z= 650 mm.
3.3. Gruppi ottici posteriori
I vincoli imposti dalla normativa per tutte le luci posteriori sono:
-distanza minima tra i bordi interni delle superfici illuminanti: 600 mm (per veicoli con fuori tutto
laterale maggiore di 1300 mm),
– altezza minima da terra: 350 mm,
La verifica del corretto posizionamento è risultata più semplice per i gruppi ottici posteriori, per i
quali si è scelta la classica forma tonda parzialmente fuori carrozzeria agli angoli superiori della
coda, comune a molti modelli del marchio Ferrari. Le funzioni di luce di arresto, luce di posizione,
C:\Users\Alessandro\Desktop\nuova relazione carrozzeria\farodietro.png
indicatore di direzione, retromarcia e fendinebbia sono stati integrati nei gruppi ottici
suddividendoli in cerchi concentrici e sfruttando la tecnologia led per gestire la forma complessa a
corona circolare di ogni settore di illuminazione. La forma del gruppo ottico verifica
automaticamente il rispetto degli angoli di illuminazione.
Figura 3.6: gruppo ottico posteriore
3.4. Cofano anteriore
La modellazione del cofano, è stata una fase fortemente critica, in quanto il disegno originale non
era più soddisfacente sia dal punto di vista estetico che funzionale, coerentemente con le parti già
modellate. E’ stata necessaria una verifica preliminare sulla suddivisione in parti della carrozzeria,
che ha evidenziato come le forme del cofano e gli sfoghi d’aria determinassero una geometria
della parte apribile complessa e probabilmente di difficile realizzazione pratica, nonché la difficoltà
C:\Users\Alessandro\Desktop\nuova relazione carrozzeria\cofano.png
nel ricavare un vano portabagagli tra i passaruota anteriori. La modellazione quindi è stata
semplificata e realizzata direttamente in 3D, conservando solo il rialzo centrale, esteticamente più
coerente con lo stile generale.
Figura 3.7: cofano anteriore
3.5. Condotti aria e radiatori
Nonostante non fosse previsto uno studio approfondito dell’aerodinamica del veicolo,
congiuntamente alle scelte stilistiche sono stati previsti quegli elementi fondamentali per
l’interazione tra veicolo e aria sia per la funzione aerodinamica sia per la funzione di
raffreddamento e aerazione.
Il primo di questi elementi interessati dalla modellazione è stato l’estrattore, del quale si è
modellata la zona terminale più in vista, integrata alla carrozzeria. Infatti, oltre alla funzione
prettamente aerodinamica, l’estrattore viene sfruttato come artificio stilistico per “alleggerire” le
forme del posteriore, quando questo risulti di notevole dimensione, in modo da rendere più
C:\Users\Alessandro\Desktop\nuova relazione carrozzeria\estrattore.png
accattivante la vista del retro della vettura. Il disegno in 2D ha subito rivelato i limiti nel poter
giudicare la forma modellata, il che ha portato anche in questo caso a modellare più agevolmente
la parte terminale dei canali dell’estrattore direttamente al CAD. La prima versione seppure
esteticamente valida entrava in contrasto con il terminale del cambio. La soluzione è stata trovata
dividendo i canali dell’estrattore in due parti, e lasciando al cento un settore di contenimento per
il carter del cambio, evitando così di dover procedere all’aumento dello sbalzo posteriore, che
avrebbe danneggiato la resa estetica globale della vettura.
Una volta modellata la geometria definitiva è stato verificato che la scatola di contenimento del
cambio rientrasse ancora nel limite imposto dall’angolo di attacco posteriore.
Ai lati dell’estrattore sono state modellate due maschere contenenti i catadiottri (posti in
posizione regolamentare, larghezza minima tra i bordi interni 600 mm, distanza massima dal fuori
tutto laterale 400 mm, altezza minima da terra 350 mm, massima 900 mm) e due terminali di
scarico per lato, posta in considerazione l’elevata cilindrata di un possibile propulsore di
equipaggiamento della vettura.
Figura 3.8: estrattore
La realizzazione delle prese d’aria è stata preceduta dal dimensionamento e posizionamento dei
radiatori necessari allo scambio termico dei fluidi motore. Presupponendo un propulsore simile a
quello delle vetture della stessa categoria di ultima produzione, è stata effettuata una ricerca sui
componenti equipaggianti tali modelli (in particolar modo sui radiatori). Dai dati rilevati è stato
effettuato un dimensionamento di media dei radiatori dell’acqua e dell’olio motore. I radiatori
sono quattro, divisi in due gruppi simmetrici rispetto all’asse longitudinale; la posizione è stata
scelta frontale, mantenendo il margine di 200 mm dal fuori tutto anteriore della zona deformabile,
in quanto in tale zona sono previste le prese d’aria di maggior superficie (Figura 3.9).
Figura 3.9: schema radiatori
Inizialmente oltre alle due prese d’aria principali previste sui bozzetti, sono state aggiunte due
ulteriori fessure di ingresso dell’aria, più esterne, per provvedere al raffreddamento dei freni
anteriori (Figura 3.12 a); successivamente però questa soluzione è stata scartata per motivi
principalmente estetici, rimandando alle prese d’aria principali, adeguatamente ridimensionate,
entrambe le funzioni (Figura 3.10).
C:\Users\Alessandro\Desktop\nuova relazione carrozzeria\prese d’aria front.png
C:\Users\Alessandro\Desktop\nuova relazione carrozzeria\presa lat.png
Figura 3.10: prese d’aria anteriori definitive
Le prese d’aria centrali sono state realizzate in posizione analoga a quella del modello originale,
ma ammodernate nella forma e aumentate in estensione per raccogliere una portata d’aria
sufficiente a garantire l’aerazione del vano motore e dei freni posteriori (Figura 3.11).
Figura 3.11: prese d’aria laterali
Successivamente è stata modellata una versione alternativa che prevedesse una presa d’aria
supplementare con la sola funzione di aerazione dei freni posteriori, anche questa scartata in
breve, in quanto difficilmente integrabile con le linee della carrozzeria. Per quanto riguarda
l’evacuazione di calore dai freni, dopo alcune proposte di ulteriori sfoghi per l’aria dietro i quattro
passaruota, si è scelto di rimandare questa funzione al fondo piatto della vettura (Figura 3.12 b,c).
C:\Users\Alessandro\Desktop\nuova relazione carrozzeria\presevecchie.jpg
C:\Users\Alessandro\Desktop\nuova relazione carrozzeria\maschere dietro.png
Figura 3.12: soluzioni scartate
L’aria calda raccolta nel vano motore viene espulsa attraverso due griglie adiacenti alle luci
posteriori, di cui sono state più volte proposte diverse versioni vagliate dal gruppo, sia sul disegno
cartaceo che sul modello 3D (Figura 3.13).
Figura 3.13: maschere d’estrazione dell’aria
3.6. Dispositivi di visione indiretta
Per il modellamento dei retrovisori esterni è stata effettuata una ricerca preliminare su quanto la
normativa vigente impone in termini di dimensionamento e collocamento (vedere PDF allegato).
Impostando un raggio di curvatura della superficie riflettente infinito (per semplicità di calcolo e
simulazione) la normativa impone:
-Area riflettente contenente un rettangolo di 40 mm x 130 mm e almeno un punto di altezza
minima di 70 mm.
– Angolo massimo tra la perpendicolare alla superficie riflettente passante per il piano degli occhi
e il piano mediano longitudinale della vettura di 55°,
C:\Users\Alessandro\Desktop\retrovisori.jpg
– Area minima visibile sulla strada: una striscia di strada posta dietro il veicolo, larga 1 metro a
partire dal fuori tutto laterale a distanza 4 metri dal piano contenente gli occhi del conducente, e
larga 5 metri a partire dal fuori tutto laterale a distanza 30 metri dal piano contenente gli occhi del
conducente (Figura 3.14).
-Estensione massima dei retrovisori esterni in posizione chiusa non superiore alla larghezza
complessiva della vettura.
Il disegno preliminare dell’area riflettente e del guscio protettivo è stata costruita imponendo il
primo vincolo. E’ stata modellata la geometria direttamente in 3D e da questa, servendosi di due
proiezioni ortogonali è stata simulata la riflessione della massima area visibile sulla strada, sia sul
piano XZ che sul piano XY. Sul piano XY l’area visibile è risultata ampiamente superiore a quella
minima imposta dalla normativa (vedi Allegato “specchietti1.jpeg”); sul piano XZ invece il primo
dimensionamento dell’area riflettente non era in grado di garantire una visuale adeguata rispetto
a quella richiesta dalla normativa. La superficie dei retrovisori quindi è stata ridimensionata
aumentandone l’altezza, e di conseguenza l’area riflettente totale, permettendo così di
raggiungere il limite dei 30 metri di strada visibile (vedi Allegato “specchietti2.jpeg”) (Figura3.15).
Infine gli indicatori di direzione laterali sono stati integrati nei gusci esterni dei retrovisori,
soluzione adottata su diverse vetture stradali, nel rispetto dell’area di posizionamento degli stessi,
imposta anch’essa dalla normativa (distanza minima da terra di 500 mm, distanza massima dal
fuori tutto anteriore 1800 mm).
Figura 3.14: minima area visibile secondo regolamentazione
C:\Users\Alessandro\Desktop\nuova relazione carrozzeria\specchietti.jpg
Figura 3.15: modellazione del retrovisore esterno
C:\Users\Alessandro\Desktop\nuova relazione carrozzeria\wireframe.jpg
4. Modellazione al CAD CatiaV5
Come descritto in precedenza la prima operazione eseguita al CAD è stata la riproduzione in 3D del
layout in ambiente di modellazione ibrida. La scala di rappresentazione è stata mantenuta
invariata (1:5) rispetto al cartaceo in 2D per avere una corrispondenza biunivoca dei riferimenti e
degli elementi rappresentati. Basandosi sul piano di forma sono stati estrapolati i dati necessari
per riportare nel 3D i punti fondamentali della carrozzeria, ricavandone le coordinate spaziali, più
un numero variabile di nodi di interpolazione per riprodurre fedelmente le linee della carrozzeria,
attraverso le curve matematiche “spline”. L’insieme delle spline ha fornito un reticolo wireframe
(Figura 4.1) sulla base del quale, in ambiente di gestione delle superfici, sono state costruite le
diverse superfici che compongono la carrozzeria.
Figura 4.1: Reticolo wireframe
In questa fase abbiamo riscontrato diversi problemi nel gestire l’interfaccia delle superfici; per una
buona resa tridimensionale infatti è stata imposta la continuità di secondo grado dove le superfici
presentavano interruzioni fittizie, ottenendo un lamierato virtuale senza imperfezioni né spigoli
vivi indesiderati.
Per un risultato ottimale a fine modellazione sono stati aggiunti tutti quegli elementi necessari alla
resa virtuale della vettura come colori, materiali, elementi complementari (cerchi, pneumatici,
terminali di scarico, targhe, etc.). Anche le targhe sono state oggetto di verifica: Le dimensioni
infatti sono imposte da normativa, è previsto obbligatoriamente un dispositivo di illuminazione di
quella posteriore, che deve trovarsi ad un’altezza minima di 300 mm; questo ha portato alla scelta
C:\Users\Alessandro\Desktop\nuova relazione carrozzeria\faseintermedia.jpg
C:\Users\Alessandro\Desktop\nuova relazione carrozzeria\risultfinale.png
di integrare la targa in uno scasso ricavato tra l’estrattore e le griglie posteriori di evacuazione
dell’aria.
Tutto questo ha aiutato a comprendere globalmente il progetto sviluppato, fornendo una resa
prospettica molto vicina alla realtà, molto più difficile da raggiungere servendosi solo dei piani di
forma. Dal modello 3D, infine, sono stati estratti i disegni tecnici costruttivi quotati e corredati
dalle sezioni trasversali in loco sui prospetti anteriore e posteriore, assiali in loco sulla pianta e
trasversali ribaltate a 90° sul fianco, che aiutano a comprendere l’andamento dei volumi nella zona
centrale della vettura, poco comprensibile dalle sole proiezioni ortogonali (Appendice 2).
Figura 4.2: fase intermedia della modellazione
Figura 4.3: risultato finale
5. Tagli di carrozzeria
Una volta fissate le linee definitive della vettura è stato possibile provvedere alla divisione della
carrozzeria nelle sue parti fisse e mobili, in modo funzionale alla produzione, all’assemblaggio e
all’interazione tra vettura e utente.
Ovviamente la suddivisione proposta è stata effettuata in base ad un’analisi preliminare, e
nell’eventualità di una reale produzione sarebbe necessaria una fase di simulazione degli
accoppiamenti tra le parti della carrozzeria e tra queste e il telaio a cui vanno ancorate. Inoltre le
parti mobili devono garantire l’assenza di interferenze e impedimenti al moto completo
desiderato. Sono di fondamentale importanza le battute tra le parti mobili e fisse, ad esempio tra
portiera ed abitacolo, da realizzare in funzione dell’isolamento, del comfort degli occupanti e della
resa estetica.
La suddivisione prevede dodici elementi (figura 5.1), alcuni dei quali (elemento verde posteriore)
possono essere ottenuti per pre-assemblaggio mediante saldatura a partire da più parti
elementari.
Sull’anteriore è presente il cofano (arancio), incernierato in prossimità del curvano, per accedere
all’eventuale vano portabagagli ricavato tre le ruote anteriori, mentre il paraurti frontale (verde) è
unico e interessa le prese d’aria, la zona sottostante i gruppi ottici e si estende lateralmente fino ai
passaruota anteriori. Al di sopra dei gruppi ottici si estende la parte di carrozzeria (viola) che
termina sotto il montante, adiacente alla portiera. Le portiere (rosa) sono incernierate
verticalmente sul lato anteriore, con apertura classica, e non comprendono il giro porta, ovvero i
finestrini scorrono nella portiera ma non sono vincolati superiormente ad essa. La parte che
compone montante, giro porta e tetto (celeste) prevede le guarnizioni di battuta dei finestrini
laterali. Dietro le portiere la carrozzeria è scomposta in due parti, che definiscono il fianco, le
pareti interne ed esterne della presa d’aria e il passaruota posteriore (giallo-verde). Tra i
passaruota si estende la copertura del vano motore, ricavata con un piano delimitato dai
prolungamenti del padiglione verso la zona posteriore. La struttura (rosa) composta dalle due
“vele” e dal piano interposto tra esse si apre per accedere al vano motore, grazie alle cerniere
previste superiormente al lunotto. Nella zona posteriore i passaruota lasciano spazio ad un’unica
parte di carrozzeria (viola) che comprende le maschere di estrazione dell’aria dal vano motore, i
terminali di scarico e lo scasso ricavato su di essa per alloggiare l’estrattore proveniente dal fondo
del veicolo.
C:\Users\Alessandro\Desktop\Senza-titolo-1.jpg
C:\Users\Alessandro\Desktop\Senza-titolo-2.jpg
Figura 5.1: suddivisione della carrozzeria
D:\ING VEICOLO\disegno di carrozzeria e componenti\carrozzeria\progetto carrozzeria Ferrari GT (250 GT LM 64 )\SS (2).jpg
6. Caratteristiche tecniche della nuova vettura
Alcune caratteristiche della vettura sono state ricavate direttamente dal layout meccanico di
partenza, altre sono state scelte nel rispetto di tre requisiti: family feeling, ovvero coerenza
stilistica con i modelli Ferrari presenti attualmente sul mercato, rispetto dei vincoli imposti dalla
normativa di omologazione e per ultimo ma non meno importante, coerenza con il design del
modello storico rievocato.
Il veicolo presenta le seguenti caratteristiche:
Propulsore: centrale-posteriore
Posti: 2
Larghezza: 1934 mm ( 2140 mm con retrovisori esterni aperti)
Lunghezza: 4304 mm
Altezza: 1270 mm
Passo: 2560 mm
Carreggiata anteriore: 1590 mm
Carreggiata Posteriore: 1576 mm
Conclusioni
L’attività progettuale di Disegno di Carrozzeria è stata per tutto il gruppo un’esperienza
impegnativa e svolta con particolare cura ed attenzione al tema trattato. Grazie all’interesse
maturato per la materia nel corso del lavoro, abbiamo avuto modo di scoprire nuovi aspetti legati
all’Ingegneria del Veicolo e di approcciare il progetto in maniera approfondita, toccando diversi
campi legati alla progettazione industriale (dal confronto con le reali normative vigenti all’utilizzo
dei moderni strumenti CAD/CAE, punti di riferimento indispensabili nelle realtà aziendali di oggi).
Nonostante alcune difficoltà decisionali riscontrate durante il percorso all’interno del gruppo di
lavoro, siamo riusciti a collaborare pienamente con un unico obiettivo comune, svolgendo ogni
compito nella prospettiva di rendere il nostro progetto della carrozzeria soddisfacente in ogni
aspetto.
C:\Users\Alessandro\Desktop\nuova relazione carrozzeria\General headlight “Hella”.jpg
Appendice 1 – Faro anabbagliante Hella
C:\Users\Alessandro\Desktop\layout-con-oscar-definitivo.jpg
Appendice 2 – Piani di forma
C:\Users\Alessandro\Desktop\carr.jpg
C:\Users\Alessandro\Desktop\sez.jpg
C:\Users\Alessandro\Desktop\tot.jpg