ESAMI 2011 DISEGNO DI CARROZZERIA – Sempre dagli studenti di Ingegneria un’ipotesi di nuova Enzo Ferrari, molto complicata e un pò “barocca”
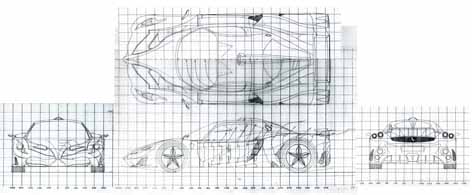
SCARICA LA TESINA COMPLETA
FACOLTÀ DI INGEGNERIA “ENZO FERRARI” CORSO DI LAUREA MAGISTRALE IN INGEGNERIA DEL VEICOLO
CORSO DI “DISEGNO DI CARROZZERIA E COMPONENTI”
DOCENTE:
Prof. Fabrizio FERRARI
STUDENTI:
Lorenzo GASPARI, Silvio GRILLI, Giovanni MATERASSI, Stefano PAPI, Maurizio TOZZOLA
ANNO ACCADEMICO 2010-2011
1. INTRODUZIONE: OBIETTIVI DELLO STUDIO
L’obiettivo del corso è quello di sviluppare un nuovo disegno di carrozzeria per una vettura sportiva stradale di casa Ferrari, partendo dal lay-out di base della “Maserati MC12” da competizione.
In particolare ci è stato chiesto di sviluppare la nuova Ferrari “Enzo”, focalizzandoci sull’estrema sportività da conferire alla vettura e traendo ispirazione dalle moderne monoposto da F1.
Si è cercato di soddisfare tali richieste tenendo conto dei requisiti ingegneristici finalizzati alla fattibilità costruttiva e al rispetto delle severe normative di omologazione per l’utilizzo stradale.
Il risultato sarà l’unione di una vettura da competizione per l’utilizzo in pista e un’ auto perfettamente idonea alla circolazione stradale.
2. FERRARI ENZO
2.1 Caratteristiche tecniche
Il concetto di “sportiva estrema”, sintesi della massima capacità tecnologica e prestazionale che la Ferrari può mettere a disposizione dei suoi clienti per un uso stradale, è rappresentato da modelli straordinari nella storia del marchio, come la 288 GTO, F40 ed F50, veri e propri esempi in epoca moderna di stato dell’arte della tecnica al servizio delle prestazioni. Comune denominatore di ciascuna di questa interpretazioni è stata, oltre all’unicità delle prestazioni, anche l’esclusività data dal limitato numero di produzione. E’ in questo filone che, nel 2002, si inserisce la “Enzo”, una vettura di eccellenza prodotta in soli 399 esemplari destinati ad un uso stradale, ma sintesi delle più avanzate conoscenze fino ad allora derivanti dall’esperienza maturata in Formula 1. Facendo leva su questo grande patrimonio tecnologico, l’obiettivo che Ferrari si pone è quello di sviluppare la “Enzo” come un sistema integrato nel quale anche il limite prestazionale ottenibile dal pilota viene innalzato attraverso un’interfaccia uomo-macchina di tipo Formula1.
2.2 Lo stile
Stilisticamente, il concetto sviluppato da Pininfarina è quello di una vettura senza compromessi, che dal punto di vista formale tagli i ponti con le impostazioni delle precedenti GTO, F40 e F50 per cercare un linguaggio nuovo e rivolto al futuro.
Nel corso dello sviluppo del progetto sono state ricercate da un lato le parentele anche visive con il mondo della F1, al quale la Enzo deve parte della sua tecnologia, dall’altro la compattezza e la leggerezza, anche attraverso l’eliminazione delle imponenti appendici aerodinamiche che caratterizzano le vetture precedenti. Il risultato è una forma complessa e sculturale che si presta a diverse letture.
Il frontale, con le due prese d’aria per i radiatori e la parte centrale rialzata, riprende chiaramente le linee del musetto della Formula 1, e molto caratteristici sono anche i gruppi ottici in moduli bi-xeno ad andamento longitudinale.
Il fianco della Enzo contrappone i volumi dei parafanghi, sul filo esterno delle ruote, ad una parte centrale più stretta e convessa che si ricollega direttamente alle “pance” della F1. Il posteriore è
come spinto verso l’alto dalla dimensione degli scivoli aerodinamici che si raccordano col sottoscocca. Il padiglione a goccia è molto compatto e rastremato verso il dietro per garantire un’elevata efficienza aerodinamica, mentre l’assenza dell’ala posteriore rende la vettura più compatta. Le portiere sono incernierate al tetto e al telaio in corrispondenza del montante A: con questa soluzione, infatti, il longherone alzandosi consente di avvicinarsi al sedile, e una parte del tetto si solleva dando modo di entrare in vettura anche dall’alto. L’apertura e chiusura delle porte è assistita da un ammortizzatore a gas. Più in generale, l’utilizzo per la carrozzeria di materiali compositi avanzati mediante realizzazione dei particolari con sandwich in fibra di carbonio e nido d’ape d’alluminio non solo ha consentito di strutturare la scocca ottenendo un deciso contenimento dei pesi, ma ha anche permesso la corretta realizzazione delle forme.
2.3 L’aerodinamica
Lo studio dell’aerodinamica come mezzo di sviluppo delle prestazioni del veicolo è sin dagli anni 60 parte integrante della cultura Ferrari. Con la Enzo, Ferrari è partita da due obiettivi di prestazione pura che rappresentassero un salto generazionale per tutte le vetture ad altissime prestazioni:
„ aumentare il limite di aderenza nelle curve medio-veloci (attraverso un incremento di deportanza);
„ mantenere contestualmente un valore molto elevato di velocità massima (oltre 350 km/h).
Di fronte a queste esigenze piuttosto contrastanti, il tema è stato affrontato in modo innovativo. Mentre infatti nelle vetture da corsa la configurazione aerodinamica viene definita sviluppando ali e accessori specifici per ogni circuito, nel caso della Enzo è stato sviluppato un concetto di aerodinamica attiva ed integrata.
Nel passaggio dal regime di medio-basse velocità a quello di alte, la meccanica, grazie a rigidezze variabili con l’altezza da terra, fa assumere alla vettura l’assetto ottimale (inteso come massimo valore di deportanza ottenuto con ripartizione ideale dei carichi). Ad un’ulteriore aumento della velocità, l’assetto viene mantenuto per mezzo dell’intervento combinato delle componenti elastiche della meccanica e del controllo attivo dei dispositivi aerodinamici. In questo modo, pur con intensità di deportanza crescenti con la velocità, la ripartizione dei carichi viene mantenuta a livello ottimale. Alle altissime velocità, l’intervento dei dispositivi aerodinamici controllati
attivamente (ali anteriore e posteriore) limita il valore massimo di carico verticale permettendo così di mantenere la vettura al di sopra di un prefissato livello minimo di altezza da terra.
In configurazione di alto carico e alte velocità si ha, rispettivamente:
1. Flap anteriori completamente ritratti (a filo con il fondoscocca);
2. Spoiler posteriore completamente estratto.
e
1. Flap anteriori completamente estratti;
2. Spoiler posteriore completamente ritratto (a filo carrozzeria).
Per far lavorare bene il fondo posteriore viene utilizzata la configurazione con muso alto e ala anteriore bassa, per recuperare carico anteriore e regolare il bilanciamento.
Il fondo posteriore è formato da due grandi diffusori ottimizzati per fornire elevati carichi ad altezze elevate da terra, senza cambiare comportamento al variare dell’assetto grazie alle grandi pinne centrali che consentono di separare il flusso al centro da quello proveniente dalle zone laterali.
Davanti alle ruote posteriori sono stati inseriti due diffusori che generano carico fra le ruote energizzando la parte di flusso normalmente in scia alla ruota anteriore. La coda della vettura è dotata di uno spoiler regolabile per ottenere l’intervallo di carichi posteriori necessario per tutto l’inviluppo di missione. La zona anteriore è invece caratterizzata dalla scelta del muso alto, al di sotto del quale scorre un canale di aria che va ad alimentare i diffusori posteriori.
2.4 Il motore
Il motore della “Enzo” è un 12 cilindri aspirato a V di 65°, di progettazione completamente nuova e derivato dalle esperienze acquisite in F1. I suoi dati caratteristici (la cui sigla di progetto è “F140”) sono una cilindrata totale di 5998 cm3, ottenuta mediante un alesaggio di 92.0 mm e corsa di 75.2 mm, per una cilindrata unitaria di 499.8 cm3 ed un rapporto di compressione pari a 11.2.
La progettazione delle teste risente a pieno dell’esperienza F1: la camera di combustione tipo pentroof, le 4 valvole per cilindro ed i condotti di aspirazione e scarico sono stati disegnati per massimizzare i coefficienti di efflusso e la velocità di combustione. La distribuzione è a 4 assi a
camme in testa con comando valvola diretto e punteria idraulica, mentre la distribuzione è a catena con rinvio centrale su ingranaggio triplo. La fase degli assi di aspirazione e scarico è continuamente variabile grazie all’intervento dei quattro variatori azionati dalla centralina in tutto il campo di funzionamento mediante impianto idraulico ad alta pressione.
Di stessa derivazione è il collettore di aspirazione a geometria variabile, con sistema di trombette telescopiche azionate mediante attuatore idraulico che ha consentito di massimizzare i valori di potenza e coppia massima.
Le prestazioni di questo motore riescono così a fornire un’elevatissima potenza, grande coppia sin dai bassi regimi e un ampio campo di utilizzo:
„ Potenza massima: 660 CV a 7800 giri/min
„ Coppia massima: 67 Kgm a 5500 giri/min
„ Coppia disponibile: 53 Kgm a 3000 giri/min
„ Regime massimo di rotazione motore: 8200 giri/min.
2.5 La trasmissione
Il gruppo cambio posteriore è in accoppiamento diretto con il motore, mediante un elemento che integra il serbatoio olio motore, la coppia conica ed il differenziale autobloccante.
Il progetto è stato sviluppato per il raggiungimento di performance estremamente sportive e prevede l’adozione di sincronizzatori a triplo cono su tutte e sei le velocità; la frizione a doppio disco di 215mm velocizza ulteriormente la dinamica del motore ed il lavoro di sincronizzazione.
Il gruppo cambio è stato sviluppato nella sola versione F1, cioè con sistema elettroidraulico che aziona il cambio stesso e la frizione. La gestione elettronica, partendo dall’azionamento mediante opportune leve posizionate dietro al volante, completa il controllo della cambiata mediando la coppia motore e la dinamica del veicolo. Le leve sono realizzate in carbonio, ottimizzate nella forma e nelle dimensioni e con possibilità di cambiata sia verso il basso sia verso l’alto per compiere un maggiore angolo di sterzata senza dover staccare le mani dal volante. Obiettivo prioritario del progetto della vettura è stato infatti l’abbattimento del tempo di cambiata (fino a 150 millisecondi), grazie anche ad una nuova strategia di controllo e a ulteriori affinamenti che nello spirito della vettura sono stati meno influenzati dai compromessi con il comfort.
2.6 Il telaio
Come detto, il telaio è stato realizzato interamente con sandwich di fibre di carbonio e nido d’ape di alluminio e ciò ha permesso di soddisfare gli elevati requisiti richiesti in termini di rigidezza, leggerezza e sicurezza.
L’obiettivo di superamento degli urti di sicurezza in condizioni offset secondo la più recente normativa (urto a 56 km/h) ha indotto ad operare con le più sofisticate metodologie CAE per l’ottimizzazione di strutture in composito, al fine di individuare la topologia ottimale della scocca e massimizzare il contributo delle pelli di rinforzo, ove necessarie, in supporto alla laminazione di base.
L’utilizzo di metodologie CAE di ottimizzazione è stato esteso anche al traliccio di supporto motore e le verifiche sperimentali hanno confermato la validità delle scelte progettuali effettuate: la rigidezza torsionale è infatti risultata superiore al target di progetto e corrispondente al valore stimato a calcolo, mentre tutti gli urti di omologazione hanno dato esito positivo alla prima prova.
2.7 Le sospensioni
La “Enzo” adotta sospensioni anteriori e posteriori indipendenti a quadrilateri articolati, con sistema antidive-antisquat per contenere il beccheggio nei trasferimenti di carico longitudinali.
La sospensione anteriore, di tipo push-rod con ammortizzatore contrapposto, è anche provvista di sollevatore per consentire una maggiore luce da terra della vettura nelle manovre di parcheggio. La sospensione posteriore risulta progettata per adattarsi al telaio con motopropulsore supportato elasticamente e conseguente telaio posteriore.
Unitamente a questo schema di sospensioni, è stato utilizzato un assetto adattativo basato su un sistema di controllo continuo dello smorzamento degli ammortizzatori: questo sistema permette di conciliare le esigenze di handling della vettura (tenuta di strada, bassa variazione di carico a terra) con le esigenze di comfort (movimenti ed accelerazioni di “cassa”, vibrazioni trasmesse al pilota) senza ricorrere a soluzioni passive (ammortizzatore standard) di compromesso.
2.8 I Freni
L’impianto frenante sviluppato specificamente da Brembo è dotato di dischi freno in materiale carbo-ceramico (CCM), per la prima volta impiegati su una vettura stradale Ferrari, dopo anni di impiego da parte della Ferrari stessa nelle competizioni di Formula 1.
Questa applicazione ha contribuito al raggiungimento dei risultati di assoluta eccellenza della Enzo in tutti i parametri di prestazione in frenata (prontezza di frenata, spazi di arresto, resistenza al fading), consentendo al tempo stesso anche una diminuzione delle masse non sospese, resa possibile dalla significativa riduzione di peso dei dischi freno (-12,5 kg rispetto ad una soluzione convenzionale).
Tutta la caratterizzazione dell’impianto frenante è stata naturalmente improntata alla massima efficacia ed efficienza, a cominciare dall’importante dimensionamento dei dischi freno (anteriori e posteriori con diametro 380 mm e spessore 34 mm) e delle pinze anteriori a 6 cilindretti e posteriori a 4 cilindretti.
3. SPECIFICHE TECNICHE DELLA VETTURA DI PARTENZA
3.1 Maserati MC12
La Maserati MC12 è una biposto coupé-spider a coda lunga e passo lungo (2800mm), di impostazione tipicamente sportivo-corsaiola e con tettuccio asportabile.
Essa dotata di un motore 12 cilindri a V di 65° di derivazione Ferrari e 5998 cc di cilindrata che eroga una potenza di 630 CV a 7500 giri al minuto ed è situato in posizione centrale/posteriore.
Lo schema di distribuzione dei pesi prevede una ripartizione di carico del 41% all‟anteriore e del 59% al posteriore. Le generose dimensioni longitudinali e trasversali, che la portano ad avere una lunghezza di 5143mm, una larghezza di 2096mm e un‟altezza di soli 1205mm, sono evidentemente il frutto di una ricerca volta all‟esaltazione delle performance della vettura più che all‟eventuale portabilità per utilizzo stradale.
Allo stesso modo prese d‟aria, sfoghi ed appendici aerodinamiche sono il frutto di una eccellente ricerca in galleria del vento mirata all‟ottimizzazione della fluidodinamica dei flussi funzionali e alla ricerca del miglior coefficiente di penetrazione aerodinamica possibile.
Per quel che concerne i materiali utilizzati, è da sottolineare che la struttura portante è in materiali compositi (fibra di carbonio e honeycomb “Nomex”) ed è abbinata a strutture di servizio anteriori e posteriori in alluminio.
Alla luce di queste premesse ne consegue che, poiché la vettura è stata progettata anche per partecipare al campionato FIA GT, le sue specifiche tecniche per quello che riguarda abitabilità, sicurezza passiva, gruppi ottici ecc., non risultano conformi alle normative standard che regolamentano la possibilità di circolazione su strada.
3.2 Parti strutturali/meccaniche oggetto di valutazioni e modifiche
Si prevede che la futura Ferrari “Enzo” sia una vettura destinata ad un mercato d‟elite, per la quale sia quindi previsto un prezzo di vendita estremamente elevato e proporzionato alla produzione limitata: per questo motivo, è stato possibile propendere per scelte e soluzioni tecniche all‟avanguardia e tecnologicamente avanzate rispetto ad una comune auto sportiva, per la quale invece il controllo dei costi di produzione (e quindi del prezzo di mercato) è un parametro fondamentale.
Il suo mercato di riferimento ha perciò permesso di curare fin nei minimi dettagli delle soluzioni meccanico-strutturali molto evolute ed assolutamente esclusive per una vettura omologata per l‟utilizzo stradale.
Prima di entrare nel dettaglio delle valutazioni tecniche effettuate al fine di rispettare la normativa di omologazione, viene proposto un elenco delle parti relative al layout meccanico di partenza che sono state oggetto di valutazioni e modifiche e che hanno influenzato le forme e le dimensioni della carrozzeria da noi proposta.
3.2.1 Radiatori del circuito di raffreddamento del motore posti all’anteriore in posizione “coricata”
La vettura di partenza presenta due radiatori montati in posizione “coricata” all‟anteriore e simmetrici rispetto all‟asse longitudinale del veicolo; essi presentano dimensioni abbastanza generose, perchè la superficie di scambio termico deve garantire la corretta efficienza dell‟impianto di raffreddamento del motore anche nelle condizioni di esercizio più critiche.
La loro posizione e dimensione è da tenere in grande considerazione nell‟ottica della realizzazione della carrozzeria, soprattutto per quanto riguarda la linea del musetto e la lunghezza complessiva della vettura. Esse risultano quindi un vincolo fondamentale per lo studio stilistico della parte anteriore della vettura.
L‟auto da noi realizzata dovrà essere adatta a un uso estremamente sportivo e potrà dunque esprimere appieno le sue prestazioni solo su circuito, ma è comunque pensata anche per un utilizzo su strada stando al rispetto delle severe normative di omologazione.
La posizione e l‟ingombro dei radiatori non hanno subito cambiamenti, ma sono state ottimizzate le prese d‟aria anteriori ed i condotti per ottenere il massimo rendimento in termini di scambio termico.
In particolare all‟anteriore si sono disposte due imponenti prese d‟aria, simmetriche rispetto al‟asse longitudinale della macchina, per avere un corretto deflusso d‟aria verso i rispettivi radiatori.
Le prese d‟aria hanno condotti dedicati ed indipendenti per ogni singolo radiatore.
Si è prevista anche un‟ulteriore presa d‟aria centrale sul musetto di dimensioni più contenute, collocata tra musetto e targa, allo scopo di aumentare il volume d‟aria diretto ai radiatori nelle condizioni di raffreddamento più critico.
Solo per questa presa infatti è stato studiato un convogliatore sdoppiato in grado di garantire un efflusso supplementare e perfettamente bilanciato di aria ad entrambi gli impianti.
L‟aria convogliata dalle prese d‟aria sui radiatori verrà fatta fuoriuscire grazie agli intagli presenti sul cofano ed in parte inviata ai passaruota anteriori. Questa consentirà, grazie alla formazione di una zona di alta pressione , un aumento della down-force sull‟avantreno vettura e quindi della stabilità e guidabilità a velocità sostenute.
La geometria invariata dei radiatori ha permesso anche di mantenere il crash-box al centro senza modificare il giusto posizionamento degli elementi ai fini del rispetto della normativa.
3.2.2 Montante A
La posizione del montante A risulta determinante per il rispetto delle norme di sicurezza e degli angoli di visibilità del guidatore.
Nonostante venga data la possibilità di apportare delle modifiche allo stesso montate, si è deciso di non apportare alcun cambiamento alla configurazione di partenza, spostando il problema sul corretto posizionamento del manichino regolamentare “Oscar”.
Così facendo, si è potuto mantenere un attacco portiera molto scavato e sagomato caratteristico delle vetture sportive, e inoltre non è stato modificato lo spazio interno all‟abitacolo, considerato già ottimale per tale tipo di vettura.
3.2.3 Captatore per l’aria presente sul tettuccio
La Maserati MC12 presenta un captatore (snorkel) sopra al tettuccio che serve a far confluire aria all‟interno del condotto di aspirazione del motore per l‟alimentazione della miscela. Non essendo esso modificabile, si è pensato di apportarvi solo piccole modifiche per consentire un miglior impatto aerodinamico. Sono state poi aggiunte delle alette di supporto laterali con funzione principalmente estetica ma poste oltre la sezione d‟ingresso in modo da non disturbare il flusso entrante con fastidiose turbolenze.
3.2.4 Radiatori dell’olio posteriori
Data la notevole cilindrata del motore predisposto per la vettura e la sua alta potenza specifica, è presente una coppia di radiatori dell‟olio nella parte posteriore, disposti simmetricamente rispetto all‟asse longitudinale del veicolo e leggermente rivolti verso l‟esterno. Analogamente a quanto visto per quelli anteriori, anche i due radiatori posteriori si trovano a dover smaltire un‟ elevata potenza termica proveniente dal motore, e quindi anche in questo caso le loro dimensioni sono considerevoli.
Il nostro studio ci impone di mantenerli invariati e la necessità di rendere disponibile un adeguato flusso d‟aria per il loro raffreddamento ha portato alla realizzazione di prese d‟aria laterali poste sui fianchi della vettura e centrate sui radiatori stessi per ottenere il massimo beneficio in termini di scambio termico. Questo per convogliare il maggior quantitativo d‟aria possibile direttamente sul radiatore dell‟olio in modo da ottimizzare il rendimento dello scambiatore e garantirgli un continuo ricambio di aria fresca. In seguito è stata predisposta un‟apertura all‟interno della presa diretta al vano motore per deviare parte del flusso direttamente sul motore.
Infine nella parte alta di ogni presa è stato ricavato un condotto dedicato allo spillamento di parte dell‟aria in ingresso e indirizzarla direttamente sull‟ala posteriore: grazie alla geometria interna del condotto, il flusso entra dal convogliatore ed esce da un presa sul cofano motore posteriore ad una velocità maggiore di quella in entrata. Il flusso sarà poi indirizzato direttamente sull‟ala posteriore per garantire un maggiore stabilità al retrotreno nelle fase di guida estrema. Si tratta infatti di un condotto a geometria variabile che può essere regolato dal pilota dall‟interno vettura, il quale potrà decidere se e quando attivarlo. Questo sistema di flussaggio aerodinamico estremamente esclusivo per una vettura stradale, trae ispirazione dalle moderne monoposto F1 e sfrutta le conoscenze sul sistema ad “ala soffiata” ricavate da Ferrari nei test su pista.
Gran parte dell‟aria in ingresso alle prese d‟aria laterali, verrà poi smaltita tramite una presa d‟aria dinamica disposta tra i due fari posteriori e protetta da una griglia traforata.
E‟ inoltre prevista una presa d‟aria statica costituita da una serie di intagli trasversali direttamente sul lunotto posteriore, grazie alla quale è possibile smaltire i vapori di benzina quando il veicolo è in fase di stazionamento, o a bassissime velocità quando il motore non è raggiunto da sufficienti portate d‟aria per il raffreddamento.
Se tali vapori non fossero smaltiti dal vano motore a veicolo fermo, si genererebbero infatti elevate pressioni sotto il cofano che risulterebbero estremamente dannose e pericolose.
La posizione e geometria delle prese laterali ha dunque profondamente inciso sulla linea del fianco e sull‟ingombro complessivo della portiera, ma si è cercato di armonizzare il tutto con lo stile della vettura, senza trascurare per questo una fluidodinamica efficiente.
3.2.5 Scatola della trasmissione
La scatola della trasmissione è un componente che incide soprattutto in termini di ingombro longitudinale e nel nostro studio è un elemento non modificabile, per cui ha solo ed esclusivamente inciso sulle dimensioni del retrotreno vettura.
Il nostro progetto, in particolare, risulta molto più corto della vettura di partenza, nonostante la scatola cambio, e si è scelto di adottare un estrattore più compatto rispetto a quello originariamente utilizzato sulla MC12.
3.2.6 Flap anteriori
All‟anteriore, nella zona delle prese d‟aria frontali per i radiatori dell‟acqua, sono presenti delle alette in composito a base di carbonio , che fungono da veri e propri flap.
Questi servono ad ottimizzare le performance della vettura in termini di carico aerodinamico all‟anteriore e in più hanno la possibilità di compiere piccoli scostamenti verticali , in un range di 20mm, in funzione della velocità e del carico aerodinamico durante la marcia. Per questi componenti non vi è però una regolazione manuale, ma un settaggio automatico in funzione della velocità, non impostabile dal pilota e il loro design richiama gli alettoni anteriori delle monoposto di F1 e punta a sottolineare la sportività della vettura.
3.2.7 Apertura sportelli laterali
Il fianco vettura è una zona di grande risalto per l‟intera struttura e la portiera di accesso all‟abitacolo è una componente di estrema importanza, sia estetica che funzionale.
Data la grande complessità strutturale del fianco, legata alle soluzioni aerodinamiche adottate, si è stati costretti ad adottare dei sistemi di apertura più complessi rispetto alle aperture convenzionali.
Infatti l‟incasso della portiera rispetto ai passaruota ed alla presa d‟aria posteriore avrebbe potuto causare alcune interferenze in fase di apertura.
Per risolvere questo problema, sono state prese in considerazione due possibili soluzioni: l‟apertura ad ali di gabbiano o l‟apertura a farfalla. Alla fine si è optato per quest‟ultima, in quanto riprende la precedente Enzo e consente al guidatore un più facile ingresso nell‟abitacolo.
Oltre a ciò, è stato necessario ideare una portiera in grado di permettere l‟abbassamento del finestrino senza che quest‟ultimo interferisca nel suo cammino con le altre parti della carrozzeria; in più si è cercato di non lasciare visibili parti del telaio o il fondo vettura una volta aperta la portiera.
Poi è stato necessario valutare la possibile posizione degli attacchi della portiera. In particolare, si è deciso di adottare due attacchi, uno formato da un giunto estendibile che abbia funzione portante sull‟intera portiera ed un altro posto sulla parte alta del montante, che svolga la sola funzione di guida per la parte alta della porta.
Come si può notare dall‟immagine del fianco vettura, la maniglia non è visibile , e in più si è deciso di rendere automatica l‟apertura delle portiere, dato che l‟enorme massa sospesa può risultare eccessiva. La porta elettroattuata è dunque apribile dall‟esterno tramite un pulsante opportunamente conformato, appositamente nascosto nella scanalatura centrale della porta, cosicché basta passare la mano nella scanalatura della portiera e azionarlo pulsante per avviare l‟apertura elettrica.
3.2.8 Apertura cofano posteriore
Diversamente dal cofano anteriore, che visto dal fianco presenta un„apertura in senso orario, quello posteriore ha un sistema di apertura più complesso per ovviare ai problemi dovuti alla spinale del condotto di aspirazione integrato nel telaio.
Questo vincolo ha imposto l‟utilizzo di una cerniera per consentire un moto roto-traslatorio del portellone in fase di apertura, per evitare l‟interferenza tra i componenti fissi e quelli mobili.
Il sistema di attuazione per l‟apertura è controllato direttamente dalla centralina ed è attivabile dall‟interno dell‟abitacolo tramite apposito pulsante.
In questa fase il portellone, prima di ruotare in senso antiorario, compie una traslazione verso l‟alto fino a raggiungere uno scostamento di 40mm pari allo spessore del portello.
4. VALUTAZIONI TECNICHE NEL RISPETTO DELLA NORMATIVA DI OMOLOGAZIONE PER LA CIRCOLAZIONE STRADALE
4.1 Posizionamento Oscar
Il primo passo per il disegno della carrozzeria è stato quello di riportare su un foglio millimetrato, in scala 1:5, gli ingombri massimi del telaio della Maserati MC12: in questo modo è stato possibile valutare il possibile posizionamento di Oscar all‟interno dell‟abitacolo per rispettare appieno le norme di omologazione.
Oscar è il manichino regolamentare di fattezze antropomorfe (altezza 1,78m), utilizzato per gli studi di abitabilità e sicurezza passiva, per cui stato necessario costruirne una copia su cartoncino in scala opportuna e renderne mobili le articolazioni mediante l‟uso di fermacampioni.
Tale copia è stata utilizzata per valutare direttamente sul disegno il corretto posizionamento del punto H, ovvero quel particolare punto del manichino in cui si immagina sia centrata l‟articolazione dell‟anca.
Disponendo degli ingombri meccanici della vettura di partenza e del posizionamento originale di Oscar, si è proceduto in primo luogo a valutare per quale posizione del punto H, ruotando il busto del manichino, non si verificasse l‟impatto della testa contro il tetto vettura o il parabrezza.
Si è deciso allora di non modificare l‟inclinazione del montante A per mantenere gli alti rendimenti aerodinamici della vettura di partenza e inoltre, avendo a che fare con una vettura sportiva, si è dato ad Oscar una posizione molto allungata e infossata. Facendo alcune prove si è trovata una posizione del punto H per la quale una rotazione del busto del manichino non comportasse interferenze con parti meccaniche della vettura.
Successivamente il manichino è stato utilizzato per valutare la posizione del punto di visuale del guidatore. Infatti le normative impongono che il guidatore abbia a disposizione un certo angolo di visuale: tale angolo viene valutato a partire dal punto di visuale (occhi del manichino) e tracciando da qui una linea parallela al suolo ed una linea obliqua direzionata verso la terra e tangente alla zona del curvano o del cofano. Per quanto riguarda la retta tangente alla zona del cofano, la normativa impone un angolo che non deve essere inferiore ai 7°, mentre per quanto riguarda la retta tangente alla zona del curvano l‟angolo non deve essere inferiore ai 5°. Infine, la normativa impone anche il rispetto di un angolo di visuale laterale minimo che deve essere di 23° in totale, di cui 7° valutati a sinistra del punto di visuale e i restanti 16° valutati a destra.
A questo punto allora ruotando il manichino attorno al punto H stabilito, si è trovata una posizione di Oscar che rispettasse tutti gli angoli di visibilità e si è verificato che per tale configurazione l‟inclinazione del busto formasse un angolo minore di 25° rispetto alla retta perpendicolare al suolo, come previsto dalle
norme. Dopodiché, si è potuto anche trovare il massimo ingombro del musetto dell‟autovettura in relazione alla visibilità dell‟oscar.
Per completezza, si riporta in tabella 4.1 l‟elenco dei dati relativi al posizionamento del manichino regolamentare e agli angoli di visibilità che ne derivano.
Le coordinate sono misurate a partire dal punto zero, che corrisponde al punto di intersezione tra la proiezione dell‟asse longitudinale del veicolo sul piano di terra (si individua così l‟asse X) e la proiezione, sempre sul piano di terra, dell‟asse passante per i centri ruota anteriori (si individua così l‟asse Y). L‟asse X è positivo verso il posteriore del veicolo, l‟asse Y è positivo verso il lato guidatore e l‟asse Z è ortogonale ad X e ad Y nel punto zero ed è positivo verso l‟alto. Le quote sono espresse in mm in scala 1:5, gli angoli in gradi.
4.2 Prime forme e dimensioni della vettura
Una volta definita la posizione del manichino, sono state abbozzate le principali forme e dimensioni della vettura.
Inizialmente sono stati rappresentati i fondamentali elementi fissi e successivamente sono stati riportati gli angoli d‟attacco anteriore e posteriore imposti dalle normative per l‟omologazione, ovvero si sono tracciate due rette inclinate di 7° uscenti dai punti di contatto tra le ruote ed il terreno: queste due rette rappresentano il limite sotto al quale la carrozzeria, in corrispondenza degli sbalzi anteriore e posteriore, non può scendere,
e sono fondamentali in quanto, se non fossero rispettate, la vettura non riuscirebbe a superare anche minime pendenze come, ad esempio, quella di un dosso o di una piccola rampa.
Infine è stata imposta un‟altezza da terra del fondo vettura di 120mm per tutto il passo, valore minimo previsto, tra l‟altro, dalla normativa.
A questo punto è stato possibile creare sulla vista laterale sinistra l‟area entro cui sviluppare l‟intera carrozzeria.
4.2.1 Sistema per la retrovisione
Pare opportuno trattare all‟interno di questo paragrafo la questione relativa alla necessità di
equipaggiare la vettura, come da normativa, con un sistema che permetta la retrovisione. Trattandosi di una vettura di altissima gamma, si è pensato di adottar,e al posto del classico specchietto retrovisore interno, un moderno sistema dotato di telecamera posteriore con relativo monitor interno all‟abitacolo (si può pensare di installare una telecamera digitale ad infrarossi per la visione notturna); questa soluzione è state adottata soprattutto perché si prevede una visibilità abbastanza ridotta attraverso il lunotto posteriore anche a causa della presenza dello snorkel, e in questo modo si riesce a risolvere tale inconveniente.
Questo particolare accorgimento potrebbe poi far parte di un pacchetto più completo, formato da sensori di parcheggio e sensore per il rilevamento della distanza di sicurezza.
Al di là di queste ultime considerazioni, che prescindono da questo studio di carrozzeria, è da sottolineare la forma e la posizione degli specchietti retrovisori esterni, che sono stati concepiti per ottenere il minor attrito aerodinamico possibile e per non ostacolare troppo il flusso d‟aria diretto verso i radiatori posteriori e la zona motore.
In figura 4.3 è rappresentato un particolare degli specchietti retrovisori.
5. STUDIO STILISTICO – FUNZIONALE DELLA NUOVA CARROZZERIA
Decise le modifiche meccaniche da apportare al telaio, il posizionamento del manichino regolamentare, le innovazioni tecnologiche da introdurre e le linee guida per il disegno della carrozzeria, si è passati alla realizzazione dei prospetti della vettura.
L‟obiettivo che ci si è prefissati è quello di realizzare una carrozzeria adatta ad una vettura estremamente sportiva, con un carattere deciso, ma che non sia solo una ricerca spasmodica dell‟estetica fine a se stessa, ma unisca alla bellezza l‟efficienza di ogni minimo particolare, come sempre è stato nello stile Ferrari.
5.1 Fianco sinistro
Si è allora proceduto a realizzare il fianco sinistro: questo ci ha permesso infatti di avere un‟ottima visione d‟insieme dell‟intera vettura, essendo di fatto molto utile a definire le prime forme e dimensioni del prototipo. Per far questo, si è prestata particolare attenzione ai diversi vincoli imposti dal telaio e dal layout meccanico in generale.
Sono stati riportati su carta millimetrata i principali ingombri della vettura, gli angoli di visuale minimi, l‟altezza minima da terra e tutti i vincoli progettuali imposti dal crash test e dalla prova del pendolo. Di conseguenza, il muso della vettura ha risentito di queste limitazioni e si è deciso allora di fare un profilo allungato che potesse al contempo risultare il più aerodinamico possibile.
Altri aspetti fondamentali di cui si è dovuto tener conto per la realizzazione del fianco sinistro sono stati la presenza del captatore snorkel e la presenza dei radiatori dell‟olio nella parte posteriore.
In relazione a ciò, si è disegnato una presa d‟aria laterale sul fianco, posta subito dietro la portiera e abbastanza centrata sui radiatori posteriori, utile sia per il raffreddamento dei radiatori stessi che del vano motore. Le dimensioni sono volutamente generose per riprendere quelle delle vetture di F1, tuttavia è stato necessario suddividerle per rispettare le norme a riguardo. Anche la divisione però non è casuale, ma è stata concepita per direzionare meglio i flussi: l‟apertura inferiore serve per portare aria al vano motore e permetterne il corretto raffreddamento, mentre le altre due permettono lo scambio termico con i radiatori dell‟olio. Parte dell‟aria catturata dall‟apertura superiore serve poi per permettere lo stallo dell‟ala posteriore e quindi garantire una maggiore velocità di punta.
I flap presenti sulla fiancata, così come la particolare conformazione della stessa, permettono di dirigere e convogliare al meglio i flussi verso le aperture laterali.
Oltre a queste prese, sono presenti due aperture in prossimità della ruota posteriore, al fine di permettere il passaggio dell‟aria attraverso il passaruota e un migliore raffreddamento dei dischi freno.
Infine, è stato deciso il taglio della carrozzeria per le portiere laterali ed il sistema più opportuno per la loro apertura, tenendo conto, come detto, delle possibile interferenze con gli altri componenti della carrozzeria.
5.2 Pianta
L‟ultima seconda vista ad essere stata realizzata è quella relativa alla semi-pianta, visibile in figura 5.7.
Un primo disegno di questa è stato realizzato riportando le misure fondamentali ricavabili dalle altre tre viste: in particolare, sono state utilizzate la lunghezza e larghezza complessive della vettura, l‟ingombro massimo del parabrezza, la posizione del canale per l‟air box posto al centro tettuccio e, ovviamente, la posizione delle ruote.
In questo prospetto, è stato possibile ideare la forma definitiva del parabrezza anteriore e del vetro posteriore, oltre che la curvatura del muso; si chiarisce poi ulteriormente la posizione dei fari anteriori, e si hanno ulteriori informazioni sulla forma della portiera e sulle effettive dimensioni del canale per il convogliamento dell‟aria al condotto di aspirazione.
5.3 Prospetti anteriore e posteriore
Una volta definita a grandi linee la vista laterale e la pianta si è passati ad un disegno di massima dei prospetti anteriore e posteriore.
Prospetto posteriore
Gli aspetti fondamentali di cui si è tenuto conto per il disegno del prospetto posteriore sono la presenza di un estrattore, i quattro terminali di scarico (due per bancata), la presenza delle prese d‟aria (una statica e una dinamica), l‟ingombro del cofano motore e la presenza del porta-targa, con relative luci per l‟illuminazione notturna.
Lo scarico è formato da condotti di dimensioni differenti due a due, posti uno sopra l‟altro e con quello superiore di diametro maggiore di quello inferiore. Tale soluzione è stata adottata per creare un‟asimmetria
in grado di conferire una linea muscolosa e originale volta a sottolineare l‟imponenza del retrotreno. Di particolare importanza per il progetto di questa parte sono anche i gruppi ottici posteriori: per questi, oltre alle minime distanze previste fra loro e dal fuori-tutto, si è prestata particolare attenzione alla loro installazione su parti non mobili della carrozzeria (da segnalare la luce del retronebbia, posizionata nella parte inferiore della vettura per riprendere le monoposto di F1).
Scendendo più nel dettaglio, troviamo riuniti in un unico sistema integrato le luci di posizione, le luci di stop e gli indicatori di direzione.
In particolare, le luci di posizione e di stop sono disposte su un doppio filamento a forma di corona circolare presente su tutti e quattro i fari posteriori. Queste corone sono poi concentriche alle luci di direzione per quanto riguarda i proiettori esterni, mentre sono concentriche alle luci di retromarcia per quanto riguarda i fari interni.
Il cofano motore, è stato realizzato con una estensione che risulta sufficiente per un‟ispezione visiva della trasmissione e del propulsore e per un„eventuale sostituzione delle parti del gruppo motore di semplice accesso.
Per eventuali operazioni di manutenzione profonda, si prevede siano asportabili tutti i pannelli di carrozzeria posti oltre la linea di battuta posteriore della portiera, in modo da accedere anche alle sospensioni e ai radiatori posteriori senza particolari difficoltà.
Il cofano motore integra poi nella parte alta di raccordo con il tettuccio, un lunotto di moderate dimensioni che, anche a causa della presenza dello snorkel, non riesce ad adempire in pieno alla funzione di porta ottica per il guidatore, il quale non ha un‟ottima visuale sia durante la normale marcia in avanti che durante le operazioni di retromarcia (infatti, come detto in precedenza, è previsto un sistema di telecamere per migliorare la visibilità posteriore).
Per quanto riguarda l‟apertura del cofano motore, si prevede un comando di rilascio all‟interno dell‟abitacolo posto sul cruscotto: tale comando svincola la serratura che collega cofano motore e telaio posteriore del veicolo e successivamente lascia liberi due martinetti a gas che permettono una lenta alzata del cofano, che consiste in pratica in una rotazione dello stesso (antioraria se pensiamo alla vista sul fianco sinistro) attorno alle cerniere di collegamento col tettuccio.
Si pensa che questo sistema di apertura “servoassistita” possa essere adatto per la vettura, nonostante le notevoli dimensioni del portellone. Infatti, supponendo che questo venga realizzato in fibra di carbonio e policarbonato ad alta resistenza (per la zona del lunotto), non si dovrebbe avere un peso tale da non poter essere sostenuto da dei comuni martinetti a gas opportunamente dimensionati e posizionati.
Quanto descritto è visibile in figura 5. e sulla semi-pianta.
Prospetto anteriore
Una volta realizzato il prospetto posteriore, siamo passati a definire quello anteriore.
I vincoli imposti dalla normativa che hanno condizionato il design del frontale vettura sono molteplici.
In primo luogo, è vincolante la posizione dei gruppi ottici anteriori. Infatti, mentre non vi sono particolari restrizioni sugli indicatori di direzione, luci di posizione e abbaglianti, esistono diversi obblighi per quello che riguarda la posizione dei proiettori anabbaglianti: questi infatti non possono essere posizionati a meno di 500mm da terra, non possono superare i 1200mm in altezza (vincolo ininfluente nel caso di una vettura sportiva), devono distare tra loro di minimo 600mm e non devono trovarsi oltre i 400mm dall‟estremità laterale dell‟autoveicolo.
Inoltre, essendo già assegnato il faro da utilizzare e i relativi ingombri dimensionali, è stato necessario trovare un posizionamento tale che la sua installazione non interferisse con gli organi meccanici vicini (radiatori, sospensioni e ruote) e ne rendesse possibile il montaggio.
La soluzione finale prevede la presenza di due gruppi ottici, per rispettare le normative: sopra i 508mm si è posizionato il proiettore luce anabbagliante, mentre inferiormente il proiettore abbagliante e gli indicatori di direzione che utilizzano luci a led. Anche per le luci di posizione sono stati usati dei led, che in questo caso corrono lungo tutta la direzione verticale e longitudinale del fanale per dare continuità tra i due gruppi ottici.
Per seguire le linee pronunciate del muso, questo proiettori sono disposti su piani sfalsati e a diverse profondità, con una forma molto particolare studiata per esaltare ulteriormente l‟aggressività della vettura. Un dettaglio del gruppo ottico da noi proposto è presente in figura 5.4.
Gli altri vincoli fondamentali che hanno condizionato la geometria del prospetto anteriore sono stati la necessaria presenza di una presa d‟aria per i radiatori e la necessità di rispettare precise normative sulla deformabilità del muso.
In particolare, in riferimento a quest‟ultimo, in Europa è stabilito che l‟altezza minima da terra della zona deformabile (o “paraurto”) sia di 445mm, sia in caso di vettura carica che di vettura scarica. Ma per rendere la vettura omologabile anche negli Stati Uniti, si è deciso di fissare quest‟altezza a 508mm da terra.
Inoltre, la normativa impone che in quest‟area deformabile non siano presenti parti mobili; di conseguenza, il cofano anteriore è stato dimensionato in modo tale che la linea più in basso sul frontale si trovi ad un‟altezza da terra minima di 508mm. La sua apertura avviene per rotazione attorno a cerniere poste in prossimità del curvano.
Anche in questo caso è previsto un comando all‟interno dell‟abitacolo, posto magari lateralmente subito sotto al volante e facilmente raggiungibile dalla mano sinistra del guidatore, e un sistema di lenta alzata con martinetti a gas; analogamente a quanto visto in precedenza per il portellone posteriore, si è pensato che, usando la fibra di carbonio anche per il cofano anteriore, tale sistema di apertura “servoassistita” possa essere adatto alla nostra vettura, senza quindi incontrare problemi di peso eccessivo.
Per quel che riguarda lo sfogo del flusso d‟aria proveniente dai radiatori anteriori, si è scelto di avere dei condotti convogliatori fino alla parte superiore dei passaruota anteriori, dove è stata concepita un‟uscita lamellare “a branchia” che in qualche modo riprenda le linee delle prese d‟aria laterali utilizzate per i radiatori dell‟olio posteriori.
Si è pensato di conferire alle lamelle una leggera inclinazione (5°) rispetto all‟orizzontale, in modo da ottenere un effetto “tettoia” che non consenta l‟ingresso di acqua nei convogliatori in caso di utilizzo sotto pioggia battente.
Nel caso il flusso di aria calda attraverso queste aperture sia insufficiente, si ritiene possibile creare una via di sfogo integrata nel fondo vettura, che renda possibile l‟estrazione dell‟aria calda dalla zona radiatori sfruttando l‟aerodinamica del pianale e dell‟estrattore posteriore.
Si è pensato infine di utilizzare un porta targa con due braccetti che si agganciano alla carrozzeria nelle vicinanze della parte centrale del muso.
Un‟immagine del prospetto anteriore è riportata in figura 5.5.
6 DIVISIONE CARROZZERIA
Disegnata la carrozzeria, è stato necessario individuare delle linee di taglio che vadano a definire le diverse parti in cui suddividerla (figure seguenti). Ci si è dapprima posti il problema della realizzazione delle diverse parti di carrozzeria, di eventuali sottosquadri e spigoli vivi, poi si è proceduto alla suddivisione vera e propria.
Quanto allo stile, si è puntato su linee aggressive, spigolose ed accentuate che hanno complicato leggermente il lavoro di separazione dei pezzi e lo studio del processo produttivo dei componenti.
La separazione della carrozzeria in varie parti non deve inoltre intaccare in alcun modo la linea della vettura con tagli troppo netti o non concordi con lo stile della vettura.
Questo insieme di fattori influisce sicuramente sulla tipologia dei componenti e sulla loro geometria e complessità ed andrà ad influenzarne sicuramente il processo produttivo.
Ma la tipologia di vettura e soprattutto il numero limitato di esemplari da produrre, ha permesso di ovviare a queste complessità progettuali con l‟utilizzo di materiali tecnologicamente avanzati, sistemi di processo al di fuori di certi standard produttivi e tecnologie di produzione non convenzionali.
Questo è stato possibile anche grazie all‟alto budget di spesa messoci a disposizione, che ha reso possibile l‟adozione di sistemi che rendono il processo quasi personalizzato ed esclusivo per molti componenti della vettura. Non si è cercato di rientrare in produzioni a basso costo o con alta produttività e bassi scarti, ma in un processo in grado di produrre componenti specifici estremamente complessi in numero limitato e difficilmente riproducibili su larga scala.
Si parla quindi di componenti la cui produzione non è automatizzabile, ma richiede il costante appoggio di un operatore che controlli ed eventualmente modifichi in loco la produzione del pezzo ed il relativo montaggio.
I materiali utilizzati sono altamente tecnologici ed utilizzati principalmente non per motivi produttivi, ma per finalità tecniche.
La maggior parte della carrozzeria si basa sull‟utilizzo della fibra di carbonio, così come il telaio, i componenti strutturalmente più sollecitati, mentre altre componenti sono in superlega leggera d‟alluminio. Le parti di carrozzeria meno sollecitate sono state pensate in composito con fibra di vetro, per l‟ ottimo rapporto leggerezza/resistenza meccanica.
Le immagini dei prospetti anteriore e posteriore mostrano la scomposizione della carrozzeria grazie al gioco di colori funzionale alla comprensione immediata delle varie componenti.
6.1 Prospetto anteriore
Partendo dall‟anteriore si possono notare i componenti principali come il cofano in rosso e la carrozzeria anteriore in verde ed azzurro.
Data la complessità di alcune parti come i contorni del gruppo ottico, si è pensato di utilizzare un concetto piuttosto diffuso che vede la produzione tramite l‟utilizzo del laser.
I componenti in lega vedono così la prima fase di formatura in stampo e tutta la finitura ed il taglio tramite moderna lavorazione a taglio laser, necessaria per realizzare l‟alloggiamento faro e altrimenti non fattibile con lavorazioni di tipo meccanico.
I componenti in blu, che hanno la sola funzione di copri-montante, saranno invece in composito in fibra di vetro e puntano ad alleggerire la struttura, dato che poco sollecitati, e verranno ricavati per semplice formatura resinosa con reticolo in fibra di vetro continua.
Infine, il paraurti e l‟alettone , rispettivamente in rosa e grigio, saranno realizzati interamente in fibra di carbonio, sia per massimizzare le prestazioni dal punto di vista tecnico/aerodinamico sia per garantire la massima leggerezza ai componenti.
Per il paraurti non vi sono grandi problemi produttivi, vista la geometria piuttosto semplice, mentre l‟alettone ha componenti di grande complessità, ed essendo pensato come intercambiabile, richiede una facile manovrabilità e facilità di montaggio. Esso richiede una lavorazione assistita da operatore, perché vede la creazione dell‟alettone in pezzi ed un assemblaggio finale tramite incollaggio, che è molto utilizzato nel campo dei compositi (per la fibra di carbonio si utilizzano particolari collanti resinosi che garantiscono ottime prestazioni meccaniche).
6.2 Prospetto posteriore
Il prospetto posteriore mette bene in evidenza la semplicità di scomposizione della vettura.
I componenti sono quattro: l‟alettone posteriore (in giallo), la carrozzeria con presa d‟aria dinamica (in viola) il paraurti (in rosso) e l‟estrattore (in grigio). La carrozzeria sarà realizzata anche in questo caso in lega leggera e, così come per i componenti all‟anteriore, sarà realizzata per stampaggio e seguente rifinitura delle aperture con taglio laser.
Il paraurti, l‟estrattore e l‟alettone saranno realizzati invece in fibra di carbonio per mantenere un buon compromesso tra resistenza e leggerezza. Data la loro complessità costruttiva, si renderanno necessari degli stampi particolarmente complessi, oltre all‟assistenza di un operatore. Anche in questo caso sono previste fasi di incollaggio soprattutto per le alette dell‟estrattore e per le staffe di fissaggio dell‟alettone.
Si è pensato poi di inserire un moderno composito ceramico avanzato per realizzare il gruppo di scarico. Questo permetterà un notevole alleggerimento ed una dispersione termica molto bassa, che eviterà problemi di surriscaldamento nella zona di uscita dei terminali a stretto contatto con le parti in fibra di carbonio. Il gruppo di scarico, data la complessità di lavorazione del composito ceramico, sarà realizzato per sinterizzazione.
6.3 Fianco
Dall‟osservazione del fianco si possono notare i componenti della portiera (in azzurro e blu), le alette (in giallo), il cofano posteriore (in bluette) e la carrozzeria posteriore (in grigio).
Per i componenti che non richiedono grandi proprietà meccaniche, si notano il tettuccio (in grigio) ed i copri-montanti (in arancione e verde). Questi componenti saranno tutti realizzati in composito per formatura, tranne il tettuccio, che sarà in lega leggera e lavorato poi al taglio laser.
Le parti di carrozzeria al posteriore ed il cofano motore saranno realizzati in lega leggera per garantire solidità e leggerezza.
Il cofano motore vede inoltre la presenza del vetro posteriore realizzato in policarbonato ed assemblato per incollaggio in fase di montaggio.
La copertura dello snorkel superiore sarà un condotto realizzato in fibra di carbonio ed assemblato anch‟esso per incollaggio.
La portiera in azzurro risulta infine essere tra i componenti più complessi della vettura per via delle scanalature sul fianco e della geometria complessiva. Dopo attenta analisi si è pensato di realizzarla in due componenti distinte: in lega l‟interno e in fibra di carbonio l‟insenatura esterna. La lega tagliata col laser consente però di realizzare praticamente qualsiasi tipo di geometria con una precisione e finitura molto alte.
La parte esterna, in azzurro scuro, invece verrà realizzata in fibra, ed ancorata al resto della portiera tramite fissaggi dall‟interno per non intaccare l‟estetica.
Si vuole infine sottolineare che la lega utilizzata non dovrà contenere, come spesso capita nel motor sport, percentuali di magnesio, essendo questo un materiale estremamente esotermico che prenderebbe fuoco durante le lavorazioni al laser.
7 PIANO DI FORMA DEFINITIVO
Una volta conclusi tutti i prospetti della vettura, il passo successivo è stato quello di ridisegnare tutte le viste non più come bozzetti, ma come disegni definitivi in scala 1:5, correggendo eventuali misure, in modo tale che tutte le forme e le dimensioni coincidessero su tutte le viste.
Sistemate tutte le discrepanze, si è potuto procedere con il completamento del piano di forma, ovvero si è passati a creare tutte quelle sezioni necessarie a definire completamente le curvature della carrozzeria nello spazio.
In particolare, sono state eseguite sezioni trasversali in loco sul prospetto anteriore e posteriore, sezioni ribaltate di 90° sul fianco sinistro ogni 200 mm lungo tutto il passo e una sezione trasversale ribaltata sul fianco del posteriore. Infine, per comprendere meglio l‟andamento del parabrezza e dei finestrini, si sono effettuate tre sezioni assiali.
7.1 Risultati finali
Si riportano infine, per completezza, le dimensioni effettive del prototipo da noi concepito:
– Lunghezza totale: 4605mm
– Larghezza totale: 2090mm
– Sbalzo anteriore: 1105mm
– Sbalzo posteriore: 700mm
– Altezza da terra del fondo vettura: 120mm
– Altezza complessiva della vettura: 1095
Nice post. I was checking continuously this blog and
I’m impressed! Extremely helpful information specifically the last part 🙂 I care for such info a
lot. I was looking for this particular info for a long time.
Thank you and good luck.